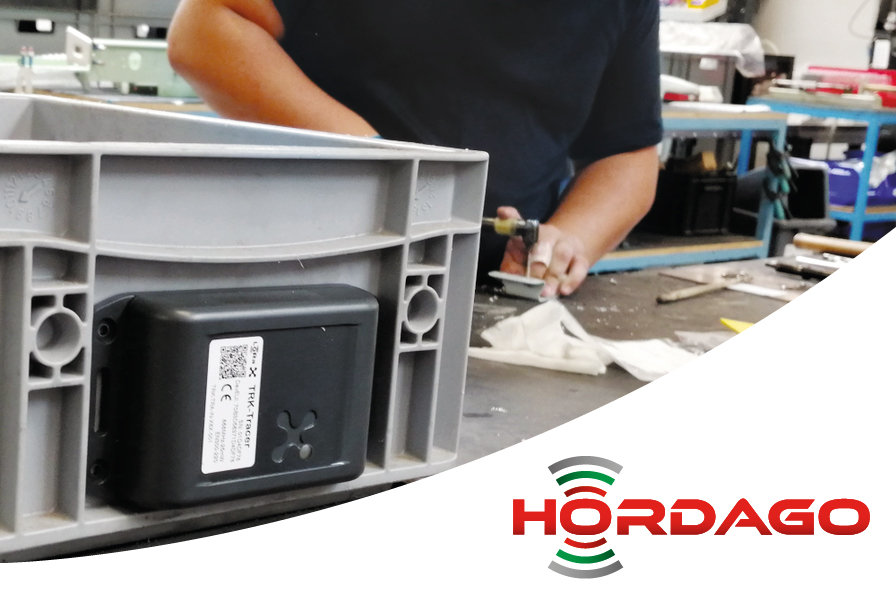
En les déployant sur ses caisses de transport de pièces, le sous-traitant de l’aéronautique réalise la plus grosse installation de capteurs LoRa en intérieur et numérise ses procédés.
Sur l’immense plateau de l’usine de Lauak, à Ahyerre (Pyrénées-Atlantiques), les opérateurs façonnent à la main des pièces qui seront intégrées dans des avions d’Airbus et de Dassault. Des formes complexes, en aluminium ou en titane, leur arrivent après avoir été usinées, découpées et pressées. Ce mouvement perpétuel d’ordres de fabrique, de références et de caisses est en train de vivre une petite révolution. Quelque 14 000 capteurs LoRa (pour long range, longue portée en français), fournis par la start-up française Ineo-Sense, viennent numériser la logistique et équiperont à la mi-septembre toutes les caisses de transport.
« Notre flux de pièces est très divers, avec des variations importantes dans la demande et un ordre de priorité qui change rapidement, constate Cédric Lynam, le responsable de la transformation digitale de l’entreprise familiale basque. La solution d’Ineo-Sense nous permet de localiser en temps réel les ordres de fabrique, donc d’avoir un stock et un temps d’utilisation précis et immédiat des caisses. » Les capteurs sont fixés à une boîte de transport de lots de pièces. « La caisse est appairée à un ordre de fabrique et nous la retrouvons facilement en la faisant clignoter », précise le responsable. C’est la première fois qu’une entreprise installe autant de capteurs LoRa en intérieur. « L’internet des objets est à la base d’une chaîne de création de valeur », observe Olivier Guilbaud, le fondateur d’Ineo-Sense. La solution qu’il commercialise, fondée sur le réseau LoRa, permet de communiquer à tout moment avec les capteurs sans perdre en autonomie d’énergie. Chose impossible auparavant.
« Nous avons cherché pendant trois ans une technologie qui nous correspondait, se souvient Cédric Lynam. Proposer une durée de vie de huit ans, en plus de la communication en temps réel, a été décisif pour notre choix. » D’après le responsable de la transformation digitale, les possibilités sont bien plus élevées que la seule gestion de stock. « Nous avons voulu rester pragmatiques et commencer par un projet avec un retour sur investissement rapide, de l’ordre de dix-huit mois. Mais plus nous en discutons, plus de nouvelles idées apparaissent. » La liste des applications envisagées est déjà longue : pointage automatique des salariés, blocage des lots défectueux, préparation semi-automatique et sécurisation des stocks, rationalisation du dialogue avec les fournisseurs… « Nous allons étudier le retour sur investissement envisagé pour chaque cas. »
Un investissement de 500 000 euros
Ce projet, d’un coût total de 500 000 euros, s’intègre dans la stratégie de numérisation du procédé industriel de l’entreprise (200 millions d’euros de chiffre d’affaires, 1 800 salariés). Baptisée Lauak 4.0, cette stratégie est dotée d’une enveloppe de 1,7 million d’euros et court jusqu’en 2021. Au tracking en temps réel et aux fiches d’instruction numériques, en cours d’installation, s’ajouteront des chariots autonomes (AGV), des cobots, des exosquelettes et un jumeau numérique. « Toutes ces innovations nous permettront, à terme, d’améliorer la qualité, de faire de la maintenance prédictive, de l’intelligence artificielle et de la simulation de flux « , envisage Cédric Lynam.
Usine Nouvelle, le 12 Janvier 2020.